Blog 207 I talked about First trip to tour China factories. In this blog I want to talk about Day one we visit a tannery.
We all met for breakfast the next morning before we headed out to the tannery. There was an amazing buffet in the dining area. It had everything you could imagine and very high quality too. It was an amazing way to start the day. We met Henry and Rob and chatted about our itinerary. Richard had it well organized, so we all were looking forward to it.
The Zappos team consisted of Richard, Fred, Aaron, James, and Myself. We arrived at the tannery in the morning after our amazing breakfast. As we approached the facility, we noticed the palm trees in front were dyed different colors as a “calling card”. We met the people running the factory and along with Henry they explained every process in great detail.
The skins arrive from all over the world in a light blue color called “wet blue” because they are raw skins that were treated in a chrome salt mixture. Have to be honest the smell of the skins wasn’t appealing. From arrival out of the containers they go through a press roller type machine to squeeze out all the moisture and water.
After most of the moisture is squeezed out, the skins are placed in large vats for a full day to go through the dye coloring process.
Once the skin goes through the dye coloring process, it will be taken out and put through the vacuum machine again to remove more water and to even out the color throughout the skin.
At this stage, the skin becomes translucent, color is brought up on the body. The skin is then placed in a machine to be waxed and sprayed lightly by pigment dye to hide the imperfections on the skins.
Skins are hung for approximately four days from the ceiling to completely dry. Once the skins are completely dried, they are pressed with a machine to imprint a leather texture to hide any lines, imperfections, and to give texture to the skins.
The skins are placed to go through a light machine, which measures the length and width of the skins. Then they are trimmed and waxed and then the skins are rolled into bundles and are ready to be shipped out.
*Suede is done the same way but on the back side of the skin.
*Nubuck is sanded down to give a softer hand.
It was a very interesting experience to see how leather is processed for footwear. Next we would be travelling to a last factory
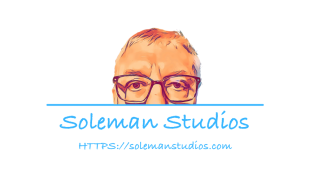
…just sharing my story and tips from my footwear career.